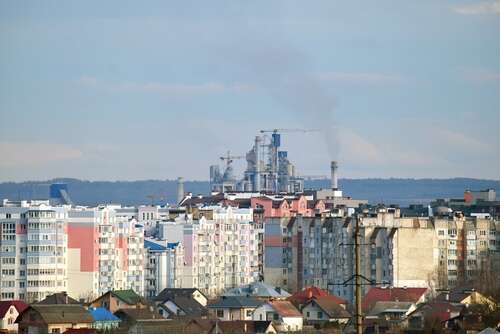
In advanced economies, one could be forgiven for thinking that there was no such thing as reindustrialisation. Contrary to popular belief, cities have never been entirely deindustrialised. Instead, even a “post-industrial” poster child like London or New York City is home to scores of businesses that produce or process material goods.

The idea of cities being ”post-industrial” and of urban manufacturing being a thing of the past was caused in part by the diminished presence and visibility of those manufacturers who stayed put rather than shutting down, relocating to suburbs, or going overseas. For much of cities’ history, manufacturers had been a staple of the urban fabric and were firmly integrated into it, both in more and less central locations.
During the 20th century this changed. Land use policies, shaped by the chaotic experiences of rapidly industrialising 19th-century cities, made it increasingly difficult for manufacturing to coexist with other uses. It was increasingly seen as outdated, dirty and disruptive – which it undeniably frequently was – and accordingly as “incompatible” with other functions. As a result, it was increasingly pushed out of more central and mixed urban areas.
In major cities dwindling space and rising land prices presented additional problems for businesses. One has to be able to afford to operate in central locations, and many businesses couldn’t, especially as towards the end of the 20th century remaining central industrial locations increasingly became the target of ambitious regeneration projects geared towards “post-industrial” uses.
Areas where the productive activity that remained was increasingly concentrated – whether for lack of alternatives or because they indeed offered favourable conditions, such as better transport connections or more space, were meanwhile increasingly confined to locations far removed from the life of the cities to which they belonged. The sector was never “dead”: what remained of it was gradually relegated to “dead” or “dead-end” locations, out of sight and thus out of mind.
For a long time, most urban planners saw nothing wrong with this. Paradoxically, not even when it had long been accepted that urban functions should, whenever possible, be brought together rather than separated, as modernist urban planning had postulated. That it is beneficial for urban spaces to be diverse and mixed has long been a truism.
Numerous books have been published on the concept and benefits of mixed-use, which today easily constitutes one of the most widely referred to and most popular planning principles there is. Surprisingly, though, material production played virtually no role in most of these and was usually also not given much thought when planners and policymakers sang the praises of mixed-use and purported to plan accordingly. To a certain extent, this remains the case today. The much-discussed 15-minute city concept, which advocates for the creation of walkable mixed-use neighbourhoods that provide a range of living, job and leisure options, pays almost no attention to manufacturing as part of the mix it postulates.
Nevertheless, change is afoot, as an increasing number of voices have emerged in recent years calling for a fresh look at urban production and the benefits of reintegrating it into the urban fabric. This is due to a re-evaluation of the sector’s value and potential for cities, as well as the substantial changes it has undergone in recent years and the rising interest it is receiving at the national and global levels.
In the face of the so-called “fourth industrial revolution” and the growing adoption of new technologies such as artificial intelligence, the internet of things, robotics and 3D printing, manufacturing is no longer seen as crisis-ridden, ailing or even moribund. Rather, it is perceived as a dynamic sector that is essential for building innovative and inclusive as well as more sustainable and resilient economies.
This view is also catching on at the urban level and as negative perceptions associating production mainly with inconveniences such as noise and pollution are increasingly dispelled by cleaner production methods, there is also a growing appetite to bring manufacturing back to areas it was pushed out of in the past.
The case for a return of manufacturing
Research shows that there are many good reasons for this. Many manufacturers, especially those at the forefront of cutting-edge manufacturing or those operating at the interface between traditional manufacturing and the creative sector, are “city affine”. They seek proximity to urban labour and consumer markets, as well as suppliers and business partners, and they value the soft and hard infrastructure that urban areas typically call their own, including their intrinsic diversity and opportunities for exchange, inspiration and innovation.
And while many manufacturers benefit from or even rely on urban locations, research also shows that their (re)location promises many benefits for said areas: it can open up new economic prospects for cities and neighbourhoods, including those affected by previous losses of industrial activity; it can help diversify urban economies, and it can create new employment opportunities for people with a range of different skills.
What’s more, is that their presence is important for other industries contributing to urban economies’ success. This has always been true, but is arguably even more so today, given the importance attributed to opportunities for quick personal connections, collaboration and exchange as prerequisites for growth and innovation. The urban economy of the 21st century is a networked economy and many industries, including much-vaunted sectors such as the cultural and high-tech industries, depend on manufacturers in one way or another, and benefit from having them close at hand.
[Read more: Does upzoning drive new development?]
And while manufacturing plays an important role in urban economic ecosystems, influencing other industries’ productivity and ability to innovate, evidence suggests that urban dwellers also value its presence. Not only is there a growing demand for locally made, customised and readily available products, and an increased interest among end consumers to connect more directly with the makers of the products they consume. Presumably because most urban dwellers are no longer involved in material production for a living, there also appears to be a growing interest to witness and experience how things get made.
The current buzz surrounding “urban making” is at least in part a result of these developments. In recent years, many cities have experienced a growth of so-called ‘maker spaces’ alongside a wave of new manufacturing start-ups targeting urban consumers and producing everything from food, clothing and textiles to furniture, bicycles, household goods and design items. For place makers and marketeers, this trend holds great promise in that it adds to the urban experience – not only of city dwellers but also of visitors – and, especially when production processes are made visible and tangible, can help make urban spaces more attractive and interesting.
With the decline of traditional brick-and-mortar retail, the contribution that not only urban making, but also manufacturing at large alongside other industrial uses can make to urban environments’ appeal, vitality and purpose is becoming an increasingly vital issue. However, arguably even more importantly, strengthening urban production also has a role to play in the transition to more sustainable growth. It helps to shorten supply chains and delivery routes, facilitates the use of greener delivery vehicles, supports the shift towards circular economies, promotes more efficient land use and helps to counter urban sprawl.
Of course, there are still many businesses that cannot be easily integrated into the urban context due to their size or the nature of their operations – or for which it simply makes more sense economically or logistically to continue to be located elsewhere. In a growing number of cases, however, a coexistence of production and other uses seems not only perfectly possible but also necessary, as many cities face increasing demand for space – for instance for housing – but are running out of suitable land.
A turning tide?
Today, calls for a reindustrialisation of cities are growing increasingly common, as is the call for a different urban model. One in which manufacturing on a larger scale is again part of the urban fabric instead of being relegated to peripherally located, typically low-density and low-quality industrial areas.
Indicative of this is that the New Leipzig Charter adopted in 2020, the EU’s key policy framework document for sustainable urban development, operates with the idea of the “productive city” as one of its guiding principles, calling for reintegration of “productive uses” and the enabling and promotion of new forms of mixed-use that provide for the production of material goods.
A similar perspective underlies the International Building Exhibition currently taking place in and around Stuttgart, Germany. Aiming to make Stuttgart and its environs a showcase for carbon-neutral, equitable, and sustainable development, it has also made the “productive city” one of its core themes and involves several projects that attempt to integrate industrial and other uses for the benefit of both.
One city that has already made a name for itself in this respect is Brussels. Here planners and politicians have for several years been endeavouring to combat the decline of manufacturing and reintegrate production into the urban fabric, drawing on the idea of the “productive city”. The banks of the Charleroi-Antwerp canal running through Brussels and the wider metropolitan region are a good example of how they go about this. The canal has been central to the region’s industry since the early 19th century, and while it has seen its share of deindustrialisation and decline, it never lost its industrial character and purpose altogether.
Instead of relying on standard urban regeneration formulas and displacing remaining industrial uses in favour of flats, offices and tourist attractions, local and regional decision-makers opted to make their preservation and strengthening a central focus of the canal banks’ revitalisation. Based on a redevelopment plan adopted in 2014, numerous projects have been implemented that aim to protect traditional manufacturers, attract new productive uses, and enable new forms of mixed-use at different scales while also enhancing the urban environment, and promoting socio-economic inclusion and cohesion.
The transformation that resulted from this is impressive in many respects, not least architecturally. Frequently realised on the basis of design competitions, many projects not only show how uses previously considered incompatible can be brought together through imaginative spatial typologies and design solutions, such as vertical factories, enabling productive uses to be stacked on top of one another close to residential and commercial sites, as well as novel industrial mixed-use concepts for buildings, individual sites and at the neighbourhood level. Instead, they also demonstrate the role that manufacturing can play in place-making, turning neglected urban spaces into vibrant places that improve quality of life for all.
None of this is to suggest that Brussels could pass as an unequivocal “success story”: It may have launched a host of pioneering projects and successfully positioned itself as a “hub for locally focussed making”. However, the region’s manufacturing economy continues to struggle and efforts to revitalise and reintegrate it into the urban fabric are not without weaknesses and drawbacks, as even commentators who are generally sympathetic to them note.
Attempts to bring together residential and productive uses do not always work out smoothly. Traditional and new productive uses at times do not so much benefit from each other as compete for territory and attention. And the ignited development dynamics at times threaten the stated goal of fostering inclusion and cohesion by putting additional pressure on, and threatening to displace, disadvantaged groups.
A renaissance of urban manufacturing from New York to London
Other examples demonstrate that efforts to make space for production rarely come without conflicts and contradictions. A case in point is the efforts to promote industrial development in New York such as the Brooklyn Army Terminal or the Made in NY Campus along the Brooklyn waterfront in Sunset Park. These are intended to boost the Big Apple as a manufacturing hub by capitalising on synergies between traditional and advanced manufacturing, as well as between manufacturing and the city’s creative and technology sectors; however, the extent to which such high-profile initiatives benefit existing residents and businesses is debatable, with some locals claiming that they erode the affordability of their traditional immigrant and working-class neighbourhood.
Such concerns cannot be dismissed out of hand, and yet efforts in New York show that decision makers view production differently than just a few years ago.
At the same time, the policy environment for the sector remains in most cities to this day a difficult one. Parts of it, such as advanced manufacturers and entrepreneurial makers are increasingly in the spotlight. Others, however, are not and in many places a lack of suitable, affordable land stands in the way of a manufacturing renaissance on a larger scale.
In London, as a recent report by the Centre for London shows, the importance of productive uses is increasingly recognised. However, instead of gaining space for them, the city continues to lose industrial land due to its ongoing repurposing for other, more profitable uses. In light of this, new mixed-use developments that earmark land for (light) industrial use, such as Wick Lane in East London, are merely a drop in the bucket and particularly land-intensive businesses and lower-value operations such as repair and recycling are struggling.
However, they are important to the functioning and life of a city and the Centre for London’s research moreover suggests that there is too little in the way of strategic, coordinated policies combining spatial planning and economic development to better support urban production and realise the potentials associated with it.
This is also true of other cities. Measures to support manufacturing may have become more extensive and imaginative, from land-use policy to workforce development programmes and branding initiatives celebrating local craftmanship and domestic production. However, there is still a gap between the much-touted significance of “productive cities” in the context of the broader need for reindustrialisation invoked in advanced economies, and the steps being taken to reinvigorate urban manufacturing and reintegrate it into cities’ urban fabric.
This was already the case before the recent disruptions of global supply chains but is even more apparent today. In fact, considering today’s multitude of crises challenging globalisation and its international division of labour, making space for manufacturing, not only but also in cities, is poised to become less a matter of want than of necessity.
The extent to which this will be the case is anyone’s guess, but there’s a case to be made for manufacturing to be given greater consideration. In cities’ political arenas, in planning, and, crucially, as part of our cities’ urban mix.
[Read more: In expensive cities, the future of residential construction is deeply uncertain]